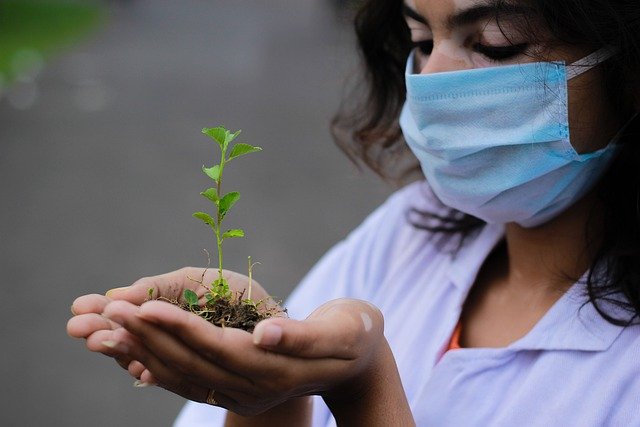
Chemical process simulation is used to understand and improve chemical or physical transformation processes to meet environmental, efficiency, and safety demands. It has become an important technology in the decision-making, operation, and engineering of the entire production system.
Chemical process simulation utilizes software tools that help predict the behavior of a chemical process. This is possible through the assistance of phase equilibrium, transport, and chemical kinetic equations.
Simulation is done during the design phase to determine how changes in equipment size, downtime, and schedule will affect the process during the actual operation.
Types of chemical process simulation
- Steady-state simulation
In the steady-state simulation, all variables remain constant regardless of the ongoing chemical process striving to change the variables. The steady-state simulation helps to design a system that achieves these requirements.
Steady-state simulation maximizes productivity as you’re able to obtain the results faster and directly. It also helps simplify the post-processing of the product. - Dynamic simulation
This allows the study of the performance, interactions, and control strategies of a process. Here, variables vary throughout the process at the startup, throughput, and shutdown.
Dynamic simulation helps study how the system behaves when variables emerge in the reaction process.
Dynamic simulation helps achieve several goals, which include:
• Reduction in energy consumption
• Determining system response to failure
• Establishing the behavior of automatic systemsTips to know simulation is the correct approach to solve a particular problem - Determining the type of problem.
If you can solve it analytically or by, use of mathematical equations, the simulation will be unnecessary. - Availability of resources.
Ensure you have qualified personnel to carry out the analysis and enough time for necessary implementations. - The costs.
Consider all the money to be used at each step of the simulation, including buying of software. The cost shouldn’t be higher than the money you’re looking to save. - Availability of data.
The data should be available or collectible to yield useful and reliable results.Conclusion
Chemical process simulation helps save time, money, and human resources that otherwise would be used when testing the design in the real-world environment. The type of simulation depends on the software in use, the complexity of the chemical process, and the size. To proceed successfully, evaluate the problem & cost and ensure there is available data and resources.